مقدمه
مدیریت ایمنی فرآیند (Process Safety Management - PSM) یک سیستم مدیریتی برای شناسایی، ارزیابی، کاهش و کنترل خطرات مربوط به مواد شیمیایی خطرناک و فرآیندهای صنعتی است. این سیستم توسط سازمانهایی مانند OSHA (اداره ایمنی و بهداشت شغلی آمریکا)، EPA (آژانس حفاظت از محیط زیست آمریکا) و سایر سازمانهای بینالمللی تنظیم شده است.
در صنایع فرآیندی مانند نفت، گاز، پتروشیمی و شیمیایی، مدیریت ایمنی فرآیند (PSM) نقش حیاتی در جلوگیری از حوادث فاجعهبار دارد. با توجه به رشد روزافزون صنایع و استفاده گسترده از مواد شیمیایی خطرناک، نهادهای بینالمللی مانند OSHA، EPA، ANSI/API، IEC و CCPS استانداردهای مشخصی برای مدیریت ایمنی، تحلیل خطرات، و کاهش پیامدهای حوادث تدوین کردهاند. هدف این مقاله بررسی این استانداردها، روشهای اجرایی، و تأثیرات آنها در افزایش سطح ایمنی صنایع است.
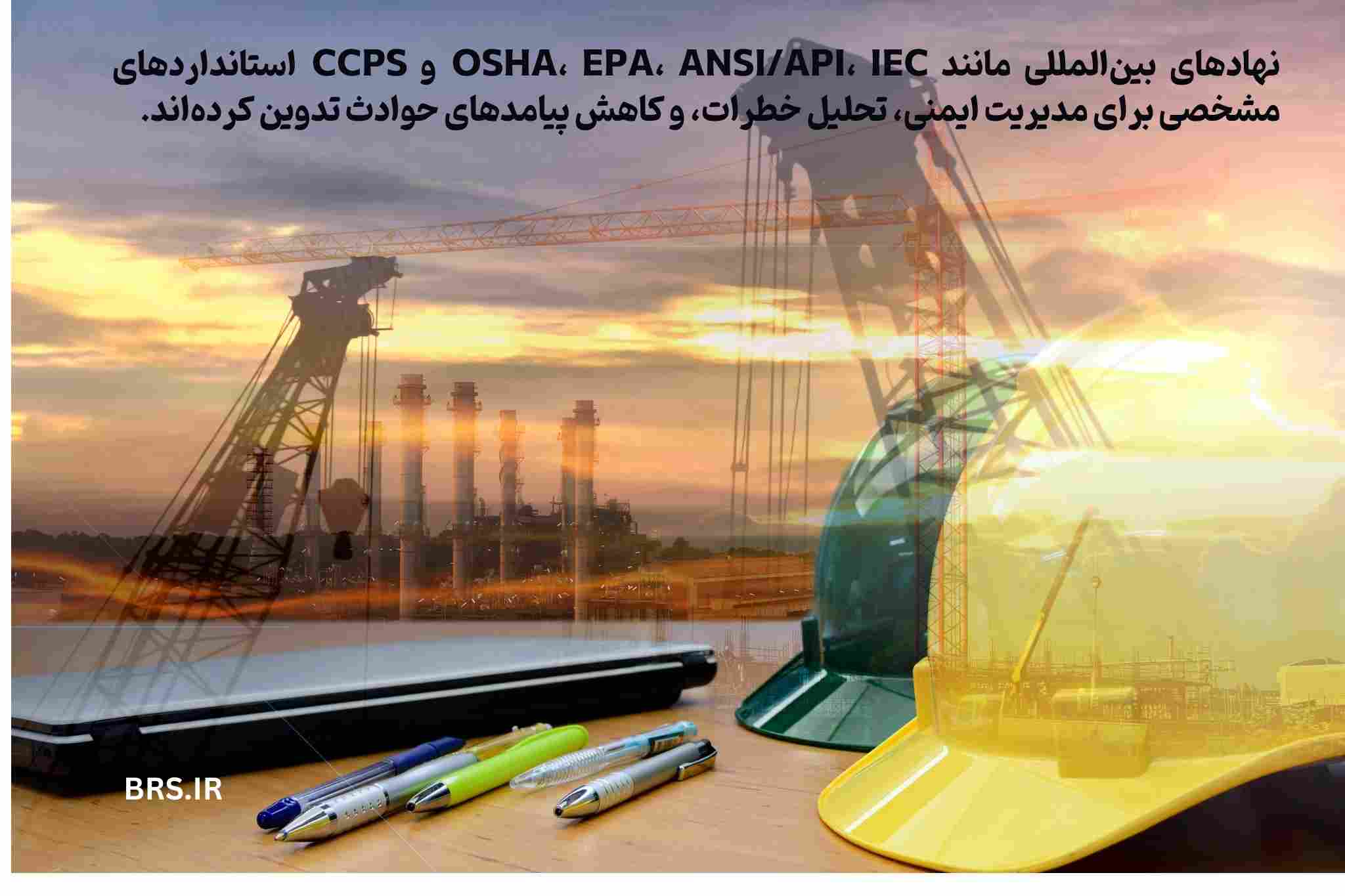
استانداردهای مهم در مدیریت ایمنی فرآیند عبارتند از :
1. استاندارد OSHA 3132 (29 CFR 1910.119) - مدیریت ایمنی فرآیند (PSM)
سازمان OSHA این استاندارد را برای مدیریت ایمنی فرآیند در صنایع دارای مواد شیمیایی خطرناک تدوین کرده است. این استاندارد بر پیشگیری از حوادث صنعتی بزرگ مانند انفجار، آتشسوزی و نشت مواد سمی تمرکز دارد.
مراحل پیادهسازی استاندارد OSHA 3132 (PSM):
✅ 1. تحلیل خطر فرآیند (PHA - Process Hazard Analysis)
شناسایی و ارزیابی خطرات مرتبط با فرآیند
استفاده از روشهای HAZOP، What-If، FMEA، LOPA و …
✅ 2. اطلاعات ایمنی فرآیند (PSI - Process Safety Information)
مستندسازی اطلاعات مرتبط با مواد شیمیایی و تجهیزات
بررسی ویژگیهای فیزیکی و شیمیایی، دیاگرامهای فرآیندی و استانداردهای طراحی
✅ 3. روشهای عملیاتی ایمن (Operating Procedures)
تعریف رویههای استاندارد عملیاتی برای فرآیندها
تضمین ایمنی در راهاندازی، خاموشی و عملیات عادی
✅ 4. مدیریت تغییرات (MOC - Management of Change)
ارزیابی تغییرات در تجهیزات، فرآیندها و کارکنان
جلوگیری از تغییرات ناایمن در سیستم
✅ 5. تحلیل ایمنی قبل از راهاندازی (PSSR - Pre-Startup Safety Review)
بررسی تمامی سیستمهای ایمنی قبل از راهاندازی یک واحد صنعتی جدید
✅ 6. صلاحیت و آموزش کارکنان
ارائه آموزشهای ایمنی و فنی به کارکنان
برگزاری آزمونهای دورهای و شبیهسازی شرایط اضطراری
✅ 7. نگهداری و تعمیرات مکانیکی (Mechanical Integrity - MI)
تست و بازرسی دورهای تجهیزات حیاتی مانند مخازن، مبدلها، ولوها و سنسورها
✅ 8. بررسی و گزارشدهی حوادث
تحلیل علتهای ریشهای حوادث (RCA - Root Cause Analysis)
تدوین اقدامات اصلاحی برای جلوگیری از تکرار حوادث
✅ 9. برنامههای واکنش اضطراری (Emergency Planning & Response)
طراحی و اجرای سناریوهای واکنش در شرایط اضطراری مانند نشت گاز یا آتشسوزی
✅ 10. ایمنی پیمانکاران (Contractor Safety)
بررسی سوابق ایمنی پیمانکاران قبل از همکاری
نظارت بر اجرای الزامات ایمنی در پروژههای پیمانکاری
✅ 11. هماهنگی با جامعه و اطلاعرسانی
برقراری ارتباط با مقامات محلی و گروههای امدادی
✅ 12. تضمین کیفیت و یکپارچگی تجهیزات (Mechanical Integrity - MI)
استفاده از سیستمهای بازرسی، نگهداری و تست تجهیزات ایمنی
✅ 13. انطباق با مقررات و ممیزیهای دورهای
انجام ممیزیهای داخلی و خارجی برای اطمینان از اجرای صحیح PSM
✅ 14. مدیریت تغییرات در دانش فرآیند
بهروزرسانی مستندات و رویههای ایمنی پس از هر تغییر
2. استاندارد EPA - RMP (40 CFR Part 68)
(Risk Management Program - برنامه مدیریت ریسک)
این استاندارد توسط آژانس حفاظت از محیط زیست آمریکا (EPA) برای کنترل خطرات مواد شیمیایی خطرناک و کاهش پیامدهای نشت آنها به محیط زیست تدوین شده است.
مراحل پیادهسازی RMP:
1️⃣ شناسایی مواد خطرناک
تعیین لیست مواد خطرناک طبق ضوابط EPA
بررسی آستانههای کمی هر ماده
2️⃣ تحلیل پیامدها و سناریوهای خطر
ارزیابی پیامدهای نشت یا انفجار
بررسی انتشار مواد در محیط و تأثیرات انسانی و زیستمحیطی
3️⃣ برنامههای پیشگیری از حوادث
توسعه و اجرای رویههای ایمنی
بررسی و نگهداری تجهیزات فرآیندی
مدیریت تغییرات (MOC)
4️⃣ برنامه واکنش اضطراری
تدوین برنامههای عملیاتی در شرایط اضطراری
تمرین و آموزش نیروهای امدادی و کارکنان
5️⃣ ثبت و گزارشدهی به EPA
ارائه اطلاعات به EPA از طریق سامانه RMP
بهروزرسانی هر 5 سال یا در صورت تغییر فرآیند
3. استاندارد ANSI/API RP 754 - شاخصهای عملکرد ایمنی فرآیند
این استاندارد توسط مؤسسه نفت آمریکا (API) و انجمن استانداردهای ملی آمریکا (ANSI) تدوین شده است و به پایش و ارزیابی عملکرد ایمنی فرآیندهای صنعتی میپردازد.
مراحل اجرایی ANSI/API RP 754:
1️⃣ تعریف شاخصهای عملکرد ایمنی
تعیین 4 سطح شاخص عملکرد برای رویدادهای ایمنی:
سطح 1: رویدادهای شدید (نشتیهای بزرگ، انفجار)
سطح 2: رویدادهای متوسط (نشتیهای کوچک، اختلالات عملیاتی)
سطح 3: رویدادهای جزئی (نقصهای ایمنی کوچک)
سطح 4: شاخصهای پیشنگر (مانند عدم رعایت رویهها)
2️⃣ جمعآوری و تجزیهوتحلیل دادهها
پایش و مستندسازی حوادث فرآیندی
تحلیل علتهای ریشهای و روندها
3️⃣ بهبود مستمر عملکرد ایمنی
اجرای اقدامات اصلاحی
آموزش و ارتقای فرهنگ ایمنی
4. استانداردهای IEC 61508 و IEC 61511 - سیستمهای ایمنی عملکردی (SIS)
این استانداردها برای ارزیابی و اجرای سیستمهای ایمنی عملکردی (Functional Safety) در صنایع فرآیندی تدوین شدهاند.
📌 IEC 61508: استاندارد کلی برای سیستمهای ایمنی عملکردی در صنایع مختلف
📌 IEC 61511: نسخهای تخصصی از IEC 61508 برای صنایع فرآیندی مانند نفت، گاز، پتروشیمی و شیمیایی
مراحل پیادهسازی IEC 61508 / IEC 61511:
1️⃣ تحلیل ریسک و تعیین سطح ایمنی موردنیاز (SIL - Safety Integrity Level)
شناسایی خطرات و ارزیابی شدت پیامدها
تعیین سطح یکپارچگی ایمنی (SIL 1 تا SIL 4)
2️⃣ طراحی سیستم ایمنی
استفاده از سیستمهای ایمنی ابزار دقیق (SIS) مانند شیرهای اضطراری و سنسورهای تشخیص نشتی
انتخاب تجهیزات مطابق با سطح SIL
3️⃣ اعتبارسنجی و آزمایش سیستم ایمنی
اجرای تستهای FAT (تست کارخانهای) و SAT (تست در محل)
ارزیابی قابلیت اطمینان سیستم
4️⃣ نگهداری و ممیزی مستمر
انجام آزمایشهای دورهای
بهروزرسانی سیستم بر اساس نیاز عملیاتی
5 - CCPS - مرکز ایمنی فرآیند شیمیایی (Center for Chemical Process Safety)
CCPS یک نهاد وابسته به انجمن مهندسان شیمی آمریکا (AIChE) است که به بهبود ایمنی فرآیند در صنایع شیمیایی و نفت و گاز کمک میکند. این سازمان راهنماهای جامعی را برای مدیریت ایمنی فرآیند منتشر کرده است.
مراحل اجرایی مدل CCPS:
📌 1. تعهد به ایمنی فرآیند (Commitment to Process Safety)
حمایت مدیریت ارشد و فرهنگ سازمانی ایمنی محور
استقرار سیاستهای ایمنی و برنامههای آموزشی
📌 2. شناخت و درک خطرات (Understanding Hazards & Risks)
شناسایی و ارزیابی خطرات با روشهای PHA، HAZOP و What-If
تحلیل دادههای حوادث گذشته برای یادگیری و پیشگیری
📌 3. مدیریت خطرات فرآیندی (Managing Risks of Process Hazards)
استفاده از سیستمهای ایمنی مانند SIS (Safety Instrumented Systems)
طراحی ایمنی تجهیزات بر اساس SIL (Safety Integrity Level)
📌 4. یادگیری و بهبود مستمر (Learning from Experience)
تحلیل و بررسی حوادث و شبهحوادث
برگزاری ممیزیهای دورهای و ارزیابی عملکرد ایمنی
مدل CCPS دارای 20 عنصر کلیدی است که در چهار دسته قرار میگیرند:
✅ تعهد سازمان به ایمنی فرآیند (Commitment to Process Safety)
✅ شناخت و ارزیابی خطرات فرآیند (Understanding Hazards & Risks)
✅ مدیریت ریسک و کاهش احتمال حوادث (Managing Risks of Process Hazards)
✅ یادگیری، بهبود مستمر و توسعه فرهنگ ایمنی (Learning from Experience)
استانداردهای مکمل و مرتبط با PSM و CCPS:
📍 ISO 45001 - سیستم مدیریت ایمنی و بهداشت شغلی (OHSMS)
چارچوبی برای بهبود ایمنی کارکنان و کاهش خطرات شغلی
📍 ISO 31000 - مدیریت ریسک
استانداردی برای شناسایی و ارزیابی ریسکهای عملیاتی
📍 IEC 61508 / IEC 61511 - سیستمهای ایمنی عملکردی
استانداردهای طراحی و نگهداری SIS (Safety Instrumented Systems)
📍 API RP 752 / API RP 753 - ایمنی واحدهای صنعتی و موبایل
استانداردهایی برای مکانیابی ایمن تجهیزات و ساختمانها در واحدهای صنعتی
📍 NFPA 654 - پیشگیری از انفجار گرد و غبار قابل اشتعال
دستورالعملهایی برای کاهش خطرات انفجار ناشی از گرد و غبار صنعتی
📍 Seveso III Directive - مقررات اتحادیه اروپا برای صنایع شیمیایی پرخطر
قوانین اتحادیه اروپا برای کنترل خطرات بزرگ در صنایع شیمیایی و پتروشیمی
نتیجهگیری
اجرای سیستماتیک مدیریت ایمنی فرآیند (PSM) نهتنها باعث کاهش احتمال حوادث صنعتی میشود، بلکه از تلفات جانی، خسارات مالی و آسیبهای زیستمحیطی نیز جلوگیری میکند. استانداردهای OSHA 3132، EPA RMP، IEC 61508/61511 و CCPS هرکدام نقش مهمی در پیشگیری از خطرات دارند و ترکیب این چارچوبها میتواند یک سیستم جامع ایمنی فرآیند ایجاد کند. با تعهد مدیریت، آموزش کارکنان، تحلیل مستمر خطرات، و استفاده از فناوریهای ایمنی، سازمانها میتوانند ایمنی خود را به سطح بالاتری ارتقا دهند و از پیامدهای ناگوار جلوگیری کنند.